Are you curious about how heatsinks are manufactured and their role in efficient heat dissipation? Look no further! In this article, we dive into the world of heatsink manufacturing, exploring the science behind their design and the crucial role they play in keeping electronic devices cool.
Heatsinks are essential components in many electronic devices, ranging from computers to smartphones and even cars. They work by dissipating the heat generated by the device, preventing overheating, and ensuring optimal performance. But how are these heat-dissipating wonders made?
From the selection of materials to the intricate manufacturing processes involved, we uncover the secrets behind creating efficient heatsinks. We'll explore the different types of heatsinks, such as passive and active designs, and discuss their advantages and applications. Additionally, we'll delve into the importance of thermal conductivity and how it affects the overall performance of a heatsink.
Join us on this journey as we unravel the science behind efficient heat dissipation and discover the fascinating world of heatsink manufacturing. Get ready to gain deeper insights into the technology that keeps our electronic devices running cool and performant.
How heatsinks work: principles of heat transfer
Heatsinks are essential components in many electronic devices, ranging from computers to smartphones and even cars. They work by dissipating the heat generated by the device, preventing overheating, and ensuring optimal performance. The principle behind their functioning is heat transfer.
Heat transfer occurs through three main processes: conduction, convection, and radiation. In the case of heatsinks, conduction plays a vital role. Heatsinks are made of materials with high thermal conductivity, such as aluminum or copper, which efficiently conduct heat away from the heat source.
To enhance the heat transfer process, heatsinks often have fins or ridges that increase the surface area exposed to the surrounding air. This increased surface area allows for better convection as the air absorbs the heat from the heatsink and carries it away. Additionally, radiation also contributes to heat dissipation, especially in situations where the heatsink is exposed to open space.
Overall, the combination of conduction, convection, and radiation ensures that heatsinks effectively dissipate heat and keep electronic devices at optimal operating temperatures.
Types of heatsinks: active vs. passive cooling
There are two main types of heatsinks: active and passive cooling. Active cooling involves the use of fans or other mechanical devices to enhance heat dissipation, while passive cooling relies solely on the heatsink design and materials for heat transfer.
Passive heatsinks are commonly found in devices with lower heat generation or where noise is a concern. They are typically made of aluminum or copper and consist of fins that increase the surface area for better heat dissipation. Passive heatsinks rely on natural convection to carry away the heat and do not require any additional power source.
Active heatsinks, on the other hand, incorporate fans or blowers to force air over the heatsink, enhancing heat dissipation. These types of heatsinks are commonly used in high-performance computers, gaming consoles, and servers, where there is a significant amount of heat to be dissipated. The combination of active cooling with efficient heatsink design allows for better heat dissipation, thus preventing overheating and ensuring optimal performance.
Materials used in heatsink manufacturing
The choice of materials in heatsink manufacturing is critical to ensure efficient heat dissipation. The two most commonly used materials are aluminum and copper, both known for their high thermal conductivity.
Aluminum heatsinks are lightweight and cost-effective, making them widely used in various electronic devices.They have good thermal conductivity but are not as effective as copper in transferring heat. However, the low cost and ease of manufacturing make aluminum heatsinks a popular choice.
Copper heatsinks, on the other hand, have excellent thermal conductivity, making them highly efficient in transferring heat away from the heat source. Copper heatsinks are often used in high-performance applications where heat dissipation is crucial, such as high-end computer processors or power electronics. However, copper heatsinks are heavier and more expensive compared to aluminum heatsinks.
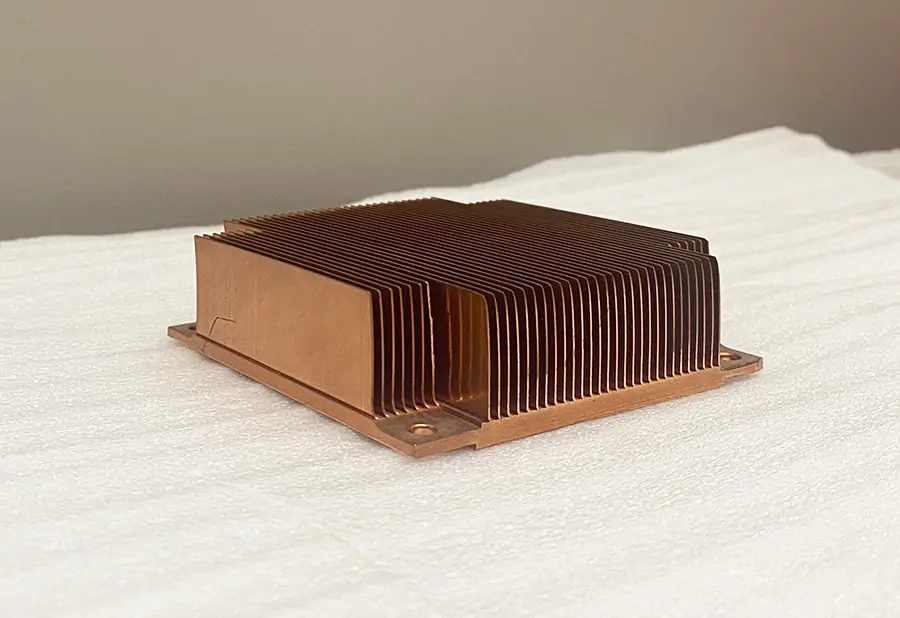
In some cases, heatsinks are made using a combination of materials, such as copper base with aluminum fins.This combination allows for efficient heat transfer from the heat source to the copper base and then dissipates the heat through the aluminum fins, balancing performance and cost.
The design process: factors to consider when designing a heatsink
Designing an efficient heatsink involves considering various factors to ensure optimal heat dissipation. Some of the key factors include:
1. Thermal resistance: The lower the thermal resistance of a heatsink, the better it is at transferring heat away from the heat source. The design should aim to minimize thermal resistance by maximizing the surface area, optimizing fin spacing, and choosing appropriate materials.
2. Airflow: The design should consider the airflow around the heatsink. Proper airflow ensures efficient heat transfer and prevents the buildup of stagnant air that can hinder heat dissipation. Factors such as fan placement, enclosure design, and orientation of the heatsink should be taken into account.
3. Compatibility: The heatsink design should be compatible with the electronic device it is intended for. Factors such as size, shape, and mounting mechanism should be considered to ensure easy integration and proper alignment with the heat source.
4. Manufacturing feasibility: The design should be manufacturable using the chosen manufacturing methods.Factors such as complexity, tolerances, and material availability should be considered to ensure cost-effective production.
By carefully considering these factors, heatsink designers can create efficient and effective solutions for heat dissipation in electronic devices.
Manufacturing methods: extrusion, die casting, and CNC machining
Heatsinks can be manufactured using various methods, each with its advantages and limitations. The three commonly used manufacturing methods for heatsinks are extrusion, die casting, and CNC machining.
Extrusion is the most common method for manufacturing heatsinks. It involves pushing molten metal, typically aluminum, through a die to create the desired shape. Extrusion allows for complex designs and precise control over the dimensions. The extruded heatsinks can then be further processed to add fins or other features for enhanced heat dissipation.
Die casting is another popular method for heatsink manufacturing. It involves injecting molten metal, such as aluminum or zinc, into a die under high pressure. Die casting offers faster production rates and can achieve intricate designs with high precision. However, die casting may result in slightly lower thermal conductivity compared to extrusion.
CNC machining, or computer numerical control machining, is a subtractive manufacturing process where a solid block of metal, such as aluminum or copper, is carved into the desired heatsink shape using precision cutting tools. CNC machining allows for highly customized heatsinks with complex geometries. However, it is a slower and more expensive manufacturing method compared to extrusion or die casting.
The choice of manufacturing method depends on factors such as design complexity, volume requirements, and cost considerations. Each method has its advantages and limitations, and manufacturers need to weigh these factors to determine the most suitable approach for heatsink production.
Quality control in heatsink manufacturing
Ensuring the quality of heatsinks is crucial to their performance and reliability. Manufacturers employ various quality control measures throughout the manufacturing process to maintain consistency and meet the required specifications.
One of the key quality control steps is material inspection. Raw materials, such as aluminum or copper,undergo rigorous testing to ensure they meet the required standards for thermal conductivity, purity, and mechanical properties. This helps ensure optimal heat transfer and overall heatsink performance.
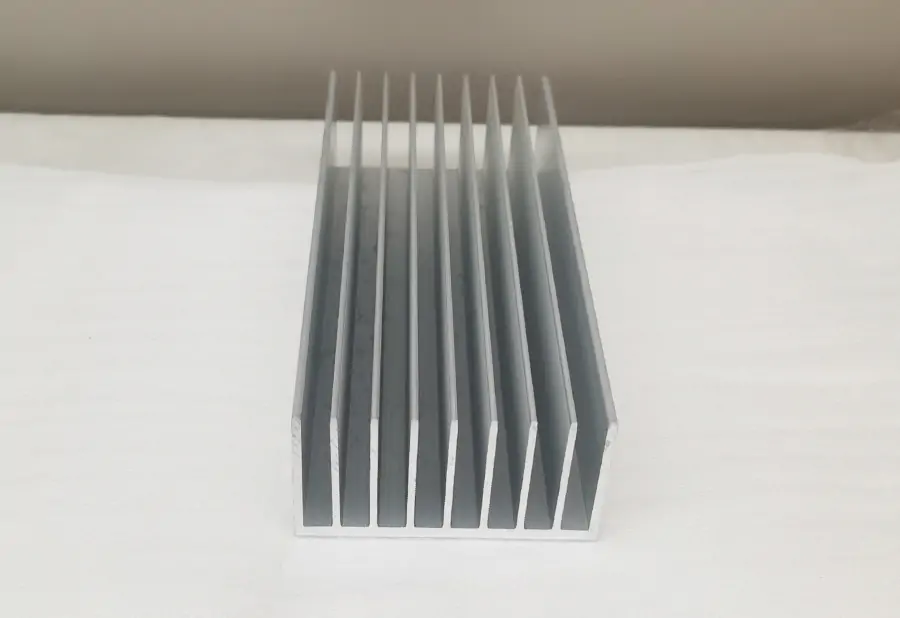
During the manufacturing process, quality control checks are conducted at various stages. These checks include dimensional inspections to ensure the heatsinks meet the specified tolerances, surface finish inspections to ensure a smooth surface for efficient heat dissipation, and visual inspections to detect any defects or irregularities.
Additionally, manufacturers may conduct thermal performance testing to verify the heat dissipation capabilities of the heatsinks. This involves subjecting the heatsinks to controlled heat sources and measuring the temperature difference across the heatsink. This testing ensures that the heatsinks are capable of effectively dissipating heat and maintaining the desired operating temperatures.
By implementing robust quality control measures, manufacturers can ensure that each heatsink meets the required specifications and performs optimally in real-world applications.
Advances in heatsink technology: liquid cooling and phase-change materials
As electronic devices become more powerful and generate higher levels of heat, traditional heatsink solutions may not always suffice. This has led to advancements in heatsink technology, with the introduction of liquid cooling and phase-change materials.
Liquid cooling involves circulating a liquid, typically water or a specialized coolant, through the heatsink to absorb and carry away the heat. Liquid cooling systems offer higher heat dissipation capabilities compared to traditional air-cooled heatsinks. These systems are commonly used in high-performance gaming computers, overclocked processors, and data centers where heat dissipation is a critical factor.
Phase-change materials (PCMs) are another innovative solution for efficient heat dissipation. PCMs are substances that can absorb and release a large amount of energy when transitioning between solid and liquid states. By incorporating PCMs into heatsinks, the heat generated by electronic devices can be efficiently absorbed and stored during the solid-state phase. As the PCM transitions to a liquid state, the stored heat is released, allowing for efficient heat dissipation. PCMs offer excellent heat storage capacity and can significantly enhance the thermal performance of heatsinks.
These advancements in heatsink technology provide more efficient and effective solutions for managing heat in high-performance electronic devices. As technology continues to evolve, we can expect further innovations in heatsink design and materials to meet the ever-increasing demands for heat dissipation.
Case studies: successful heatsink designs in various industries
Heatsinks play a vital role in numerous industries where heat dissipation is essential for optimal performance and reliability. Let's take a look at a few case studies showcasing successful heatsink designs in different applications.
Conclusion: the future of heatsink manufacturing and its impact on technology.
Heatsinks are critical components in electronic devices, ensuring efficient heat dissipation and preventing overheating. As electronic devices continue to evolve and become more powerful, the demand for advanced heatsink solutions will continue to grow.
The future of heatsink manufacturing holds exciting prospects, with ongoing advancements in materials,design, and manufacturing techniques. New materials with even higher thermal conductivity, such as graphene, may further enhance heat transfer capabilities. Advanced manufacturing methods, such as additive manufacturing, may enable the creation of complex heatsink designs with optimized internal structures for improved heat dissipation.
Additionally, the integration of heatsinks with other cooling technologies, such as liquid cooling and phase-change materials, will provide even more efficient solutions for managing heat in high-performance electronic devices.
Heatsink manufacturing will continue to play a crucial role in shaping the future of technology. By pushing the boundaries of design and leveraging innovative materials and manufacturing techniques, manufacturers can create heatsinks that meet the ever-increasing demands for efficient heat dissipation. As a result, electronic devices will continue to perform optimally, ensuring reliable operation and enhanced user experiences.