Large aluminum heatsinks play a crucial role in the tech industry, providing both thermal management and increased performance for electronic devices. These innovative components are designed to efficiently dissipate heat generated by semiconductors and other heat-generating components, ensuring optimal operating temperatures and preventing overheating issues.
With advancements in technology and the growing demand for high-performance devices, the need for effective heat management has become paramount. Large aluminum heatsinks offer numerous benefits,including excellent thermal conductivity, lightweight construction, and durability. They are widely used in various applications, such as computer processors, power amplifiers, LED lights, and industrial machinery.
The use of large aluminum heatsinks significantly enhances the overall performance and reliability of electronic devices. By efficiently transferring heat away from critical components, these heatsinks help prevent thermal throttling and extend the lifespan of the device. Moreover, they reduce the risk of temperature-related failures, ensuring consistent and stable performance even under demanding conditions.
In conclusion, large aluminum heatsinks are essential components in the tech industry, providing effective thermal management and optimizing the performance of electronic devices. As technology continues to advance, the demand for these heatsinks will only continue to grow, making them a vital asset in the ever-evolving world of technology.
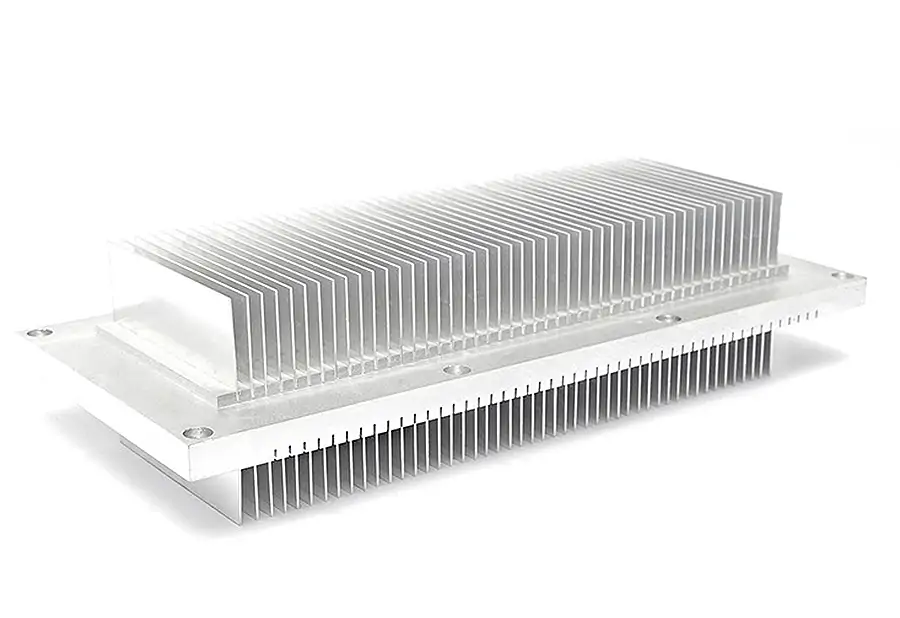
Importance of Heat Dissipation in the Tech Industry
In the fast-paced world of technology, heat dissipation is a critical factor in ensuring the optimal performance and longevity of electronic devices. As electronic components become smaller and more powerful, they generate more heat, which can lead to performance degradation and even permanent damage if not effectively managed.
Large aluminum heatsinks play a vital role in dissipating the excess heat generated by high-performance processors, graphics cards, and other heat-intensive components. By providing a large surface area, these heatsinks maximize the contact between the device and the surrounding air, facilitating the transfer of heat away from the critical components.
In addition to preventing overheating, effective heat dissipation also helps maintain consistent performance.When electronic devices operate at high temperatures, they are more prone to thermal throttling, a process in which the device reduces its performance to avoid further heat buildup. By keeping temperatures in check,large aluminum heatsinks enable devices to operate at their maximum potential, delivering optimal performance even during intense workloads.
Furthermore, heat dissipation is crucial for the longevity and reliability of electronic devices. Excessive heat can lead to the degradation of internal components, such as capacitors and transistors, which can result in premature failure. By effectively managing heat, large aluminum heatsinks help extend the lifespan of electronic devices, reducing the need for frequent replacements and saving costs for both consumers and manufacturers.
Benefits of Using Large Aluminum Heatsinks
Large aluminum heatsinks offer a wide range of benefits that make them the preferred choice for heat management in the tech industry. These benefits include:
### 1. Excellent Thermal Conductivity
Aluminum has excellent thermal conductivity, meaning it can efficiently transfer heat from the heat-generating components to the surrounding environment. This property allows large aluminum heatsinks to effectively dissipate heat, keeping the device's temperature within the acceptable range.
Compared to other materials commonly used for heatsinks, such as copper, aluminum offers a cost-effective solution without compromising performance. Its high thermal conductivity ensures efficient heat transfer while keeping the weight of the heatsink relatively low.
### 2. Lightweight Construction
Large aluminum heatsinks are lightweight, making them suitable for applications where weight is a concern,such as laptops and portable devices. The lightweight nature of aluminum heatsinks allows for easy installation and minimizes the overall weight of the device, without sacrificing thermal performance.
Additionally, the lightweight construction of aluminum heatsinks reduces strain on the device's mounting mechanism, ensuring a secure and long-lasting attachment.
### 3. Durability and Corrosion Resistance
Aluminum heatsinks are known for their durability and corrosion resistance. Aluminum naturally forms a thin oxide layer on its surface, providing protection against corrosion and ensuring the longevity of the heatsink.
This corrosion resistance is particularly important in applications where the heatsink may be exposed to harsh environments or moisture, such as outdoor LED lighting or industrial machinery. The ability of aluminum heatsinks to withstand these conditions makes them a reliable choice for demanding applications.
Applications of Large Aluminum Heatsinks in Computer Hardware
Large aluminum heatsinks find extensive use in computer hardware, where heat dissipation is crucial for optimal performance. These heatsinks are commonly employed in the following computer components:
### 1. Processors
Processors, also known as central processing units (CPUs), are the brain of a computer. They perform complex calculations and execute instructions, generating significant heat in the process. To prevent overheating and maintain the CPU's performance, large aluminum heatsinks with integrated heat pipes and cooling fans are often used.
The large surface area of these heatsinks allows for efficient heat dissipation, while the heat pipes facilitate the transfer of heat from the CPU to the heatsink. The cooling fans further enhance the airflow, ensuring effective heat management even during heavy workloads.
### 2. Graphics Cards
Graphics cards, also known as GPUs (Graphics Processing Units), are responsible for rendering images and videos on computer screens. Similar to CPUs, GPUs generate a substantial amount of heat during intensive graphics processing tasks.
To maintain optimal performance and prevent thermal throttling, large aluminum heatsinks with multiple heat pipes and cooling fans are commonly used in graphics cards. These heatsinks efficiently dissipate the heat generated by the GPU, allowing for smooth and uninterrupted graphics processing.
### 3. Power Amplifiers
Power amplifiers are essential components in audio systems, providing amplified signals to speakers or headphones. These amplifiers can generate significant heat, especially when operating at high power levels.
To prevent thermal damage and ensure reliable performance, large aluminum heatsinks are utilized in power amplifiers. The heatsinks effectively dissipate the heat generated by the amplifier's power transistors, allowing for extended operation without overheating issues.
Applications of Large Aluminum Heatsinks in LED Lighting
LED lighting has become increasingly popular due to its energy efficiency and long lifespan. However, LEDs can generate heat, which can affect their performance and longevity. Large aluminum heatsinks are commonly employed in LED lighting systems to manage the heat generated by the LEDs.
### 1. Streetlights and Outdoor Lighting
Streetlights and outdoor lighting fixtures often utilize high-power LEDs to provide bright illumination. These high-power LEDs can generate a significant amount of heat, especially when operating at maximum brightness for extended periods.
Large aluminum heatsinks effectively dissipate the heat generated by high-power LEDs, ensuring optimal performance and extending the lifespan of the LEDs. The heatsinks can be integrated into the lighting fixtures' design, allowing for efficient heat management without compromising aesthetics.
### 2. Indoor Lighting
In indoor lighting applications, such as commercial buildings and residential homes, LED bulbs are commonly used to provide energy-efficient illumination. While LED bulbs generate less heat compared to high-power LEDs, heat management is still important to maintain their performance and longevity.
Large aluminum heatsinks integrated into LED bulbs help dissipate the heat generated by the LEDs, ensuring consistent brightness and extending the lifespan of the bulbs. These heatsinks are designed to be compact and lightweight, allowing for easy integration into various bulb designs.
Applications of Large Aluminum Heatsinks in Power Electronics
Power electronics, including inverters, motor drives, and power supplies, require efficient heat dissipation to ensure reliable operation. Large aluminum heatsinks are widely used in power electronics to manage the heat generated by high-power electronic components.
### 1. Inverters
Inverters are essential components in solar energy systems, converting the DC (direct current) power generated by solar panels into AC (alternating current) power for use in homes and buildings. Inverters can generate significant heat, especially during high-power conversion.
Large aluminum heatsinks with integrated cooling fans are commonly used in inverters to dissipate the heat generated by power transistors and other high-power components. The heatsinks ensure that the inverter operates within acceptable temperature limits, preventing overheating and extending the lifespan of the device.
### 2. Motor Drives
Motor drives control the speed and torque of electric motors, making them essential in various applications,including industrial machinery, electric vehicles, and home appliances. Motor drives can generate substantial heat, especially when operating at high power levels or in demanding environments.
Large aluminum heatsinks with customized designs are employed in motor drives to effectively dissipate the heat generated by power transistors and other heat-intensive components. The heatsinks ensure reliable operation and prevent thermal damage to the motor drives, allowing for extended use in demanding applications.
Factors to Consider When Choosing Large Aluminum Heatsinks
When selecting large aluminum heatsinks for specific applications, several factors should be taken into consideration to ensure optimal performance and compatibility. These factors include:
### 1. Thermal Conductivity
The thermal conductivity of the aluminum heatsink determines its ability to efficiently transfer heat away from the heat-generating components. Higher thermal conductivity allows for more effective heat dissipation,ensuring optimal operating temperatures.
### 2. Surface Area
The surface area of the heatsink directly affects its ability to dissipate heat. A larger surface area provides more contact with the surrounding air, allowing for better heat transfer. The surface area can be increased through the use of fins, heat pipes, or extended designs.
### 3. Mounting Mechanism
The mounting mechanism of the heatsink should be compatible with the device or component it is intended to cool. Different devices may require specific mounting options, such as screws, clips, or adhesive thermal pads. It is essential to ensure a secure and proper attachment to prevent any movement or detachment during operation.
### 4. Size and Form Factor
The size and form factor of the heatsink should be suitable for the available space and design constraints of the application. It is important to consider the dimensions and clearance requirements to ensure proper installation and efficient heat dissipation.
### 5. Environmental Conditions
The operating environment of the application should be taken into account when selecting large aluminum heatsinks. Harsh environments, high humidity, or exposure to chemicals may require heatsinks with additional corrosion resistance or protective coatings.
How to Properly Install Large Aluminum Heatsinks
Proper installation of large aluminum heatsinks is crucial to ensure effective heat dissipation and reliable operation of electronic devices. The following steps outline the general procedure for installing large aluminum heatsinks:
1. Prepare the Surface: Clean the surface of the heat-generating component, ensuring it is free from dust,debris, or thermal interface material residue.
2. Apply Thermal Interface Material (TIM): Apply a thin layer of thermal interface material, such as thermal paste or thermal pads, onto the surface of the heat-generating component. This helps improve thermal conductivity and fills any microscopic gaps between the component and the heatsink.
3. Position the Heatsink: Carefully position the large aluminum heatsink onto the heat-generating component,ensuring proper alignment and contact with the thermal interface material.
4. Secure the Heatsink: Depending on the mounting mechanism, secure the heatsink in place using screws,clips, or adhesive thermal pads. Follow the manufacturer's instructions for the specific mounting method.
5. Test and Monitor: After installation, test the electronic device to ensure proper functioning and monitor the temperature to verify effective heat dissipation. If necessary, adjust the installation or consider additional cooling solutions.
Common Misconceptions about Large Aluminum Heatsinks
Despite their widespread use and proven effectiveness, there are some common misconceptions surrounding large aluminum heatsinks. It is important to address these misconceptions to ensure accurate understanding:
### 1. Bigger is Always Better
While large aluminum heatsinks generally offer better heat dissipation due to their increased surface area,bigger is not always better. The size of the heatsink should be chosen based on the specific requirements of the application. Oversized heatsinks may not fit into the available space or may cause interference with other components.
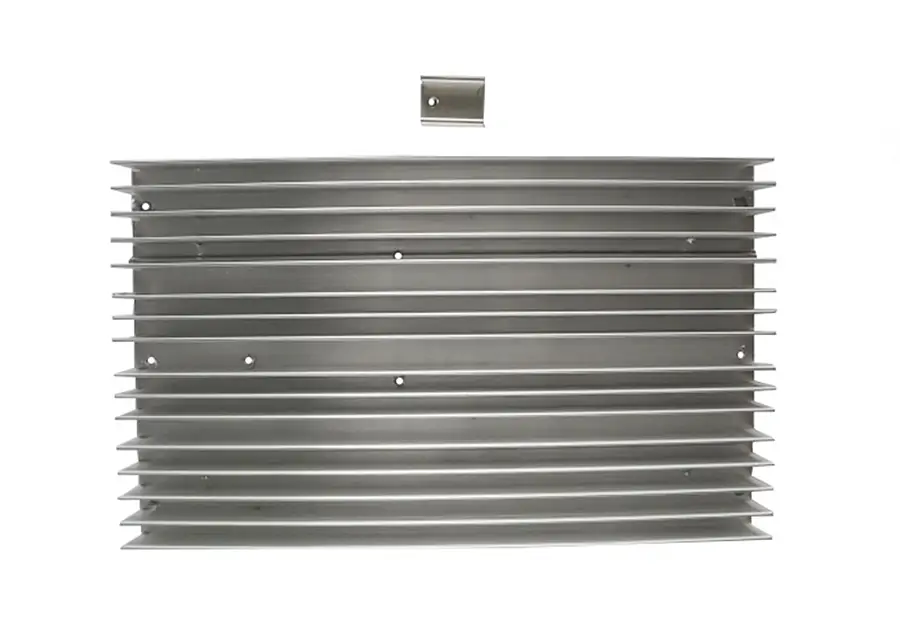
### 2. All Aluminum Heatsinks are the Same
Not all aluminum heatsinks are created equal. The thermal conductivity, design, and overall quality can vary between different manufacturers and models. It is essential to consider the specific requirements of the application and select a heatsink that meets those requirements.
### 3. Heatsinks Eliminate the Need for Active Cooling
While large aluminum heatsinks can significantly improve heat dissipation, they may not always eliminate the need for active cooling, such as cooling fans. In applications with high-power components or demanding conditions, a combination of passive and active cooling methods may be necessary to ensure optimal temperature management.