From Design to Assembly: A Deep Dive into Heatsink Manufacturing Process
If you've ever wondered how those sleek, metal devices that keep your electronics cool are made, then you're in for a treat. In this article, we'll take you on a fascinating journey through the entire heatsink manufacturing process, from design to assembly.
Heatsinks are vital components in electronic devices that dissipate heat and prevent overheating, ultimately ensuring optimal performance and longevity. But how are they actually made? It all starts with the design phase, where engineers meticulously plan the dimensions, materials, and specifications to meet the specific requirements of each device. Then comes the manufacturing process, involving precise machining, extrusion, or casting techniques to shape and form the heatsinks with utmost precision.
Once the heatsinks are formed, they undergo various finishing processes like anodizing or coating to enhance their appearance, durability, and corrosion resistance. Finally, the assembly stage brings everything together, integrating the heatsinks seamlessly into the electronic devices.
Join us as we dive deep into the intricate world of heatsink manufacturing, unraveling the precise steps and innovative techniques behind this crucial component of modern technology.
Importance of heatsinks in electronic devices
Heatsinks are vital components in electronic devices that dissipate heat and prevent overheating, ultimately ensuring optimal performance and longevity. Without heatsinks, electronic devices would be prone to damage and failure due to excessive heat buildup. The efficient cooling provided by heatsinks allows electronic components to operate within their temperature limits, maximizing their lifespan and reliability.
Heatsinks come in various shapes and sizes, depending on the specific requirements of the electronic device they are intended for. Whether it's a small heatsink for a smartphone or a large heatsink for a server, the purpose remains the same - to transfer heat away from the electronic components and dissipate it into the surrounding environment.
Heatsink manufacturing process overview
The manufacturing process of heatsinks involves several intricate steps, each contributing to the final product's functionality and quality. It all starts with the design phase, where engineers meticulously plan the dimensions, materials, and specifications to meet the specific requirements of each device.
Designing a heatsink: considerations and techniques
Designing a heatsink requires careful consideration of various factors, including thermal requirements, space constraints, and manufacturing feasibility. Engineers utilize advanced computer-aided design (CAD) software to create precise 3D models of the heatsinks, allowing them to simulate heat transfer and optimize the design for maximum efficiency.
The design phase also involves selecting the appropriate manufacturing technique, such as extrusion, casting, or machining, based on factors like cost, complexity, and material properties. Each technique has its advantages and limitations, and the choice depends on the specific application and desired heatsink characteristics.
Material selection for heatsinks
Choosing the right material for heatsinks is crucial to their performance and durability. Heat conductivity, weight, corrosion resistance, and cost are some of the key factors considered when selecting materials. Aluminum and copper are commonly used materials due to their excellent thermal conductivity.
Aluminum heatsinks are lightweight, cost-effective, and widely used in consumer electronics. Copper heatsinks, on the other hand, have superior thermal conductivity but are heavier and more expensive. Other materials like graphite, ceramic, and composite materials are also employed for specialized applications.
Machining and forming heatsink components
Once the heatsink design is finalized, the manufacturing process begins with machining or forming the heatsink components. Machining involves removing excess material using cutting tools to shape the heatsink according to the design specifications. This process requires precision equipment like CNC machines to achieve the desired dimensions and surface finish.
Extrusion is another common technique used for manufacturing heatsinks. In extrusion, a heated billet of aluminum or other suitable material is forced through a die to create the desired shape. This method allows for complex designs and high production volumes, making it ideal for mass manufacturing.
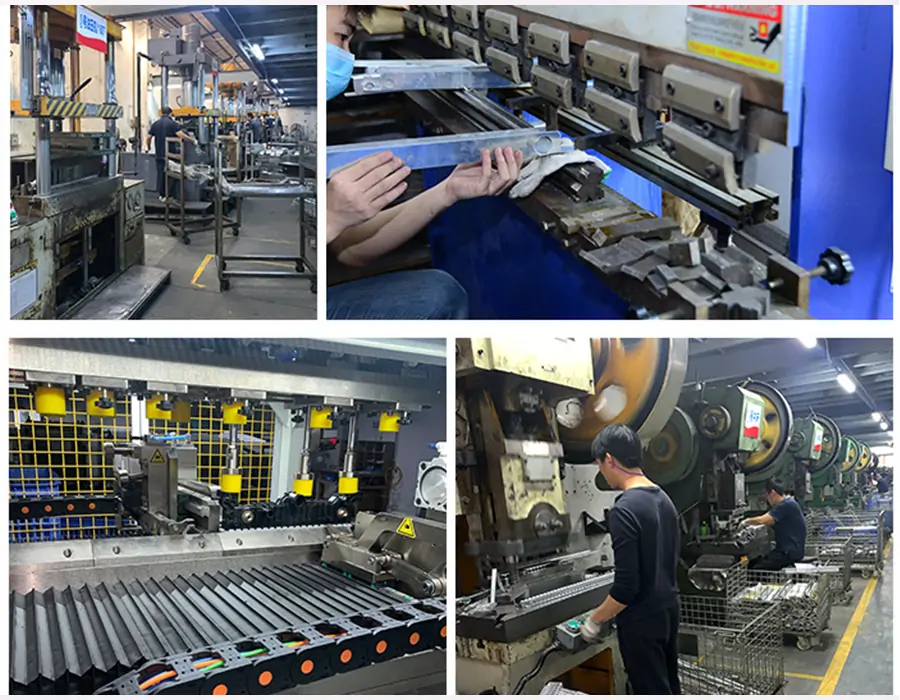
Casting is employed for more intricate heatsink designs that cannot be achieved through machining or extrusion. The molten metal is poured into a mold, where it solidifies and takes the shape of the heatsink.Casting enables the production of heatsinks with intricate internal fin structures and complex geometries.
Finishing touches: surface treatment and coating
Once the heatsinks are formed, they undergo various finishing processes to enhance their appearance, durability, and corrosion resistance. Anodizing is a common surface treatment technique used to create a protective oxide layer on aluminum heatsinks. This layer not only improves corrosion resistance but also provides a surface suitable for dyeing or painting.
Coating is another method used to enhance heatsink performance and protect them from environmental factors. Thermal spray coatings, such as ceramic or metal coatings, can be applied to improve heat transfer and reduce surface oxidation. Additionally, powder coating or electrostatic painting can be used for aesthetic purposes and to provide a protective layer.
Assembly of heatsinks and integration into electronic devices
The assembly stage brings everything together, integrating the heatsinks seamlessly into the electronic devices. Adhesive bonding or mechanical fasteners like screws or clips are used to secure the heatsinks to the electronic components. Thermal interface materials, such as thermal pads or thermal grease, are applied to ensure efficient heat transfer between the component and the heatsink.
During the assembly process, other components like fans or heat pipes may be incorporated to further enhance the cooling capacity of the heatsinks. These additional components work in conjunction with the heatsinks to dissipate heat and maintain optimal operating temperatures.
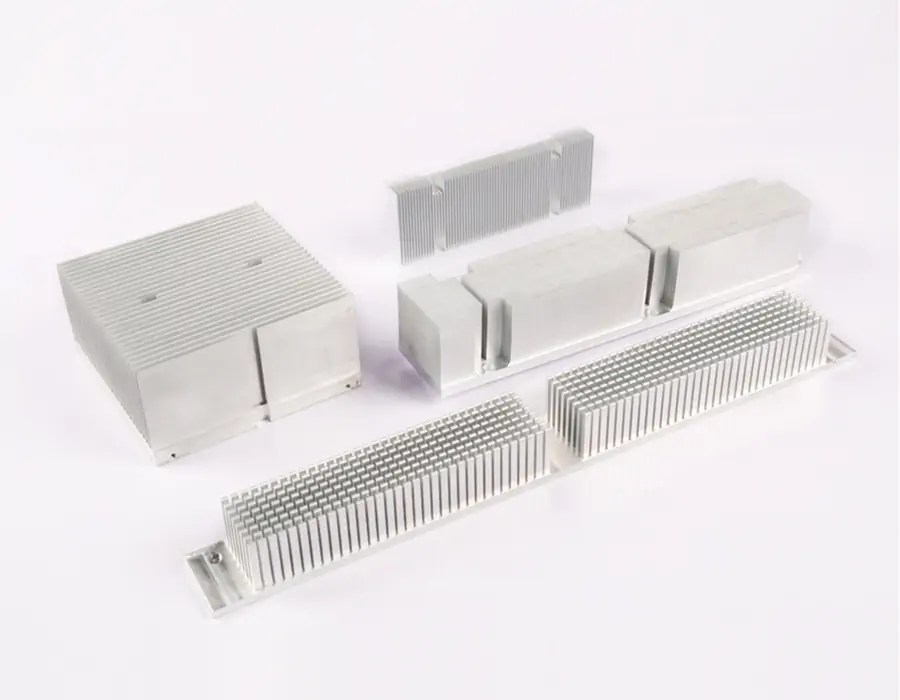
Quality control and testing in heatsink manufacturing
Quality control is an essential aspect of heatsink manufacturing to ensure that each heatsink meets the required specifications and performance standards. Various testing methods like thermal imaging, thermal resistance measurement, and thermal cycling are employed to evaluate the heatsinks' thermal performance and reliability.
Additionally, visual inspection, dimensional checks, and surface quality assessments are carried out to verify the heatsinks' overall quality and adherence to design specifications. Strict quality control measures help identify any defects or inconsistencies in the manufacturing process and ensure that only the highest-quality heatsinks are delivered to customers.
Conclusion: the future of heatsink manufacturing
The field of heatsink manufacturing is constantly evolving, driven by advancements in materials, design techniques, and manufacturing processes. As electronic devices become more compact and powerful, the demand for efficient and innovative heatsinks continues to grow.
Future developments may include the use of advanced materials like carbon nanotubes or graphene for improved thermal conductivity. Additive manufacturing techniques, such as 3D printing, may also revolutionize heatsink production, allowing for highly customized designs and rapid prototyping.
In conclusion, heatsink manufacturing is a complex and intricate process that plays a crucial role in ensuring the optimal performance and longevity of electronic devices. By understanding the design considerations, manufacturing techniques, and finishing processes involved, we gain a deeper appreciation for the vital component that keeps our electronics cool and reliable.