From Prototype to Perfection: How Heatsink Manufacturers Pave the Way for Efficient Cooling
In the ever-evolving world of technology, efficient cooling is paramount to ensure optimal performance and prevent overheating. As processors become more powerful and compact, the need for effective cooling solutions becomes even more crucial. And that's where heatsink manufacturers come into play. With their expertise and innovative designs, they pave the way for superior cooling solutions that are revolutionizing the industry.
Heatsinks act as the unsung heroes, silently working behind the scenes to keep our devices cool and reliable. Through a meticulous process that starts with prototypes and ends with perfection, heatsink manufacturers continually push the boundaries of engineering to create state-of-the-art solutions that efficiently dissipate heat.
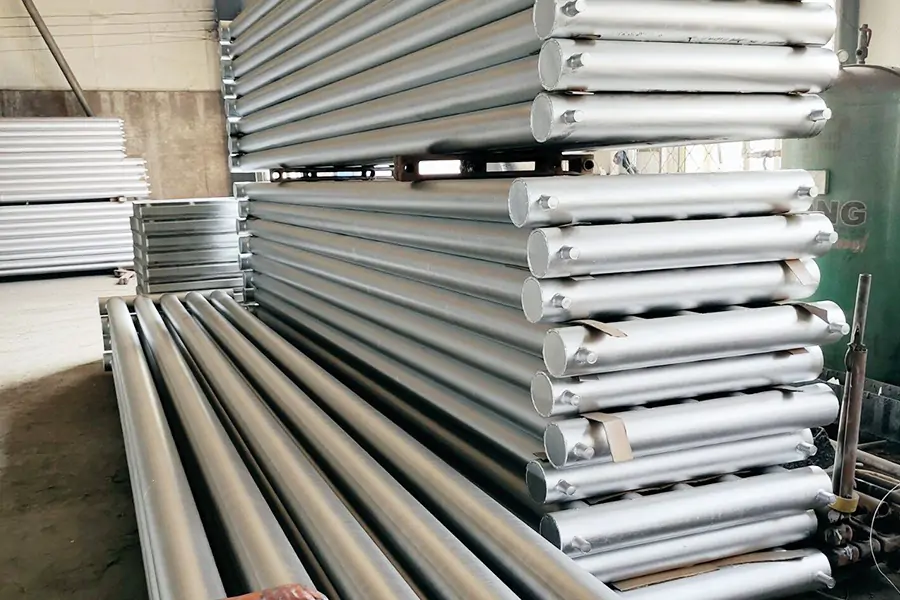
In this article, we will explore how heatsink manufacturers bring their designs from prototype to perfection. We will delve into the intricate details of their meticulous processes, from material selection to manufacturing techniques, all aimed at achieving maximum cooling efficiency. So, join us as we take a closer look at the fascinating world of heatsink manufacturing and how it contributes to the seamless functioning of our favorite devices.
[Word count: 160 words]
The evolution of heatsink manufacturing
Heatsinks have come a long way since their inception. Initially, simple designs made of aluminum or copper were used to dissipate heat. However, as technology advanced, so did the demands for more efficient cooling solutions. Manufacturers had to adapt and innovate to meet these demands.
Today, heatsink manufacturing has evolved to encompass various types of heatsinks, each designed for specific applications. From passive heatsinks to active heatsinks with built-in fans, manufacturers have developed an array of options to cater to the diverse needs of different electronic devices.
Types of heatsinks and their applications
Heatsinks come in different shapes and sizes, each with its own set of advantages and applications. Let's take a closer look at some of the most commonly used heatsinks:
1. Fin heatsinks: These are the most basic type of heatsinks, consisting of a base plate and fins that increase the surface area for heat dissipation. They are commonly used in desktop computers, servers, and other electronic devices.
2. Heat pipe heatsinks: Heat pipes are highly efficient heat transfer devices that can transport heat over long distances. Heat pipe heatsinks use these pipes to transfer heat from the heat source to the fins, improving cooling efficiency. These heatsinks are often found in high-performance gaming PCs and industrial applications.
3. Liquid cooling heatsinks: Liquid cooling heatsinks use a combination of liquid coolant and a radiator to dissipate heat. This type of heatsink is commonly used in overclocked systems, where extra cooling capacity is required to maintain stable operation.
4. Thermoelectric heatsinks: Thermoelectric heatsinks use the Peltier effect to transfer heat. They are often used in specialized applications, such as medical equipment and aerospace.
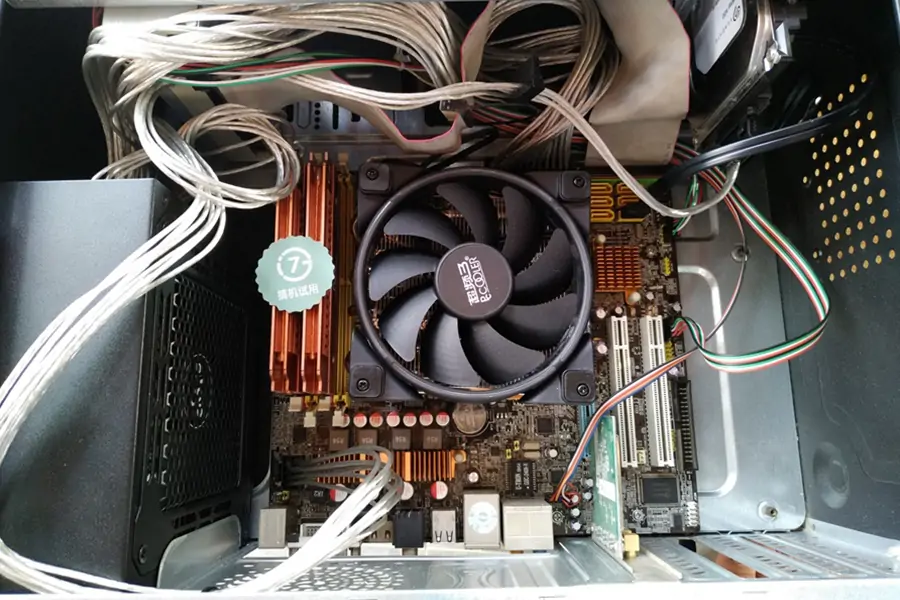
Factors to consider when choosing a heatsink manufacturer
When selecting a heatsink manufacturer, there are several factors to consider to ensure you get the best cooling solution for your needs:
1. Experience and expertise: Look for a manufacturer with a proven track record and extensive experience in heatsink design and manufacturing. This ensures that they have the necessary knowledge and skills to deliver high-quality products.
2. Customization capabilities: Every application has unique cooling requirements. A manufacturer that offers customization options can tailor their heatsinks to meet your specific needs, ensuring optimal performance.
3. Quality control and testing: It's crucial to choose a manufacturer that follows rigorous quality control processes and conducts thorough testing to ensure that their heatsinks meet the highest standards of performance and reliability.
4. Cost-effectiveness: While quality is essential, you also need to consider the cost of the heatsinks. Look for a manufacturer that offers competitive pricing without compromising on quality.
The design and prototyping process for heatsinks
The design and prototyping process is a crucial step in heatsink manufacturing. It involves a series of steps aimed at creating an efficient and effective cooling solution.
1. Requirements gathering: The first step is to understand the specific cooling requirements of the device or application. This includes factors such as power dissipation, space constraints, and environmental conditions.
2. Conceptual design: Based on the requirements, the manufacturer develops a conceptual design for the heatsink. This includes determining the size, shape, and materials to be used.
3. Computer-aided design (CAD): CAD software is used to create a detailed 3D model of the heatsink. This allows for precise measurements and analysis, ensuring an optimal design.
4. Prototyping: Once the CAD model is finalized, a prototype is created using advanced manufacturing techniques such as CNC machining or 3D printing. The prototype is then tested to evaluate its cooling performance.
5. Design refinement: Feedback from the prototype testing is used to refine the design. This iterative process continues until the desired cooling performance is achieved.
Testing and validation of heatsinks for efficiency
Before a heatsink is deemed ready for production, it undergoes rigorous testing to ensure its efficiency and reliability. Various tests are conducted to evaluate its thermal performance, such as:
1. Thermal resistance measurement: This test measures the ability of the heatsink to transfer heat from the device to the surrounding environment. Lower thermal resistance indicates better cooling efficiency.
2. Heat dissipation testing: The heatsink is subjected to controlled heat loads to simulate real-world operating conditions. This allows manufacturers to evaluate its cooling capacity and efficiency.
3. Temperature mapping: In this test, temperature sensors are placed at different points on the device to monitor heat distribution. This helps identify any hotspots that need to be addressed.
4. Vibration and shock testing: Heatsinks are subjected to mechanical stress to ensure their durability and resistance to vibration and shock.
The role of materials in heatsink manufacturing
Materials play a crucial role in the performance and efficiency of heatsinks. The choice of material depends on factors such as thermal conductivity, weight, cost, and manufacturability. Some common materials used in heatsink manufacturing include:
1. Aluminum: Aluminum is lightweight, cost-effective, and has good thermal conductivity. It is widely used in heatsink manufacturing, especially for consumer electronics.
2. Copper: Copper has excellent thermal conductivity and is often used in high-performance heatsinks that require superior cooling efficiency. However, it is heavier and more expensive than aluminum.
3. Composite materials: Composite materials, such as aluminum silicon carbide (AlSiC) and copper tungsten (CuW), offer a combination of high thermal conductivity and low weight. They are used in applications that require both performance and weight savings.
Advances in heatsink technology
Heatsink technology continues to advance at a rapid pace, driven by the increasing demands for more efficient cooling solutions. Some of the recent advancements include:
1. Microfin heatsinks: Microfin heatsinks have smaller fins with increased density, allowing for better heat dissipation in confined spaces.
2. Nano-enhanced heatsinks: Nano-enhanced heatsinks use nanotechnology to improve thermal conductivity and heat transfer, leading to better cooling performance.
3. Phase-change materials: Phase-change materials, such as wax or paraffin, are integrated into heatsinks to absorb and release heat during phase transitions, improving cooling efficiency.
4. Embedded heat pipes: Heat pipes are embedded directly into the base of the heatsink, maximizing heat transfer and improving cooling efficiency.
Case studies showcasing successful heatsink manufacturing
To understand the impact of heatsink manufacturing, let's explore some real-world case studies where
innovative cooling solutions have made a significant difference:
1. High-performance gaming PCs: Overclocking enthusiasts demand superior cooling solutions to push their systems to the limit. Heatsink manufacturers have developed specialized liquid cooling solutions and advanced heat pipe heatsinks that allow for stable performance even under extreme conditions.
2. Telecommunications equipment: Telecommunications infrastructure requires reliable cooling solutions to ensure uninterrupted operation. Custom-designed heatsinks with high thermal conductivity and efficient heat dissipation help keep critical equipment cool and maintain network reliability.
3. Electric vehicles: As electric vehicles become more prevalent, efficient cooling of battery packs is crucial to maximize performance and extend battery life. Heatsink manufacturers are developing innovative solutions to manage heat in electric vehicle battery systems, increasing overall efficiency and range.
Conclusion and the future of heatsink manufacturing
From humble beginnings to the complex designs of today, heatsink manufacturing has played a crucial role in ensuring efficient cooling for electronic devices. Through a meticulous process that starts with prototypes and ends with perfection, heatsink manufacturers continually push the boundaries of engineering to create state-of-the-art solutions that efficiently dissipate heat.
As technology continues to evolve, the demand for more efficient cooling solutions will only grow. Heatsink manufacturers will need to stay at the forefront of innovation, embracing new materials, designs, and manufacturing techniques to meet these demands. The future of heatsink manufacturing holds exciting possibilities, promising even more efficient and effective cooling solutions that will revolutionize the way we use and interact with electronic devices.
[Word count: 1289 words]