Introducing 'Unlocking the Potential of Heatsinks: A Deep Dive into the Manufacturing Process' – an illuminating article that delves into the intricate world of heatsink manufacturing. As technology continues to advance at an unprecedented pace, the demand for efficient cooling solutions grows exponentially. Heatsinks,with their ability to dissipate heat and keep crucial components cool, play a pivotal role in ensuring optimal performance and longevity.
In this comprehensive article, we explore the manufacturing process behind heatsinks, uncovering the secrets that enable them to efficiently transfer heat away from electronic devices. From the selection of raw materials,such as aluminum or copper, to the intricate designs and manufacturing techniques, we leave no stone unturned.
Whether you're an electronics enthusiast, an engineer, or simply curious about the technology that powers our gadgets, this article offers invaluable insights into the science and artistry behind heatsink manufacturing. By understanding the nuances of this process, you can uncover hidden potential and make informed decisions to optimize cooling solutions for your unique needs.
Join us as we embark on a deep dive into the world of heatsinks, unlocking their potential and demystifying the manufacturing behind these unsung heroes of the technological world.
Importance of heatsinks in electronic devices
Heatsinks are essential components in electronic devices, serving the crucial purpose of dissipating heat generated by the internal components. As electronic devices become more powerful and compact, the need for effective cooling solutions becomes even more critical. Without proper heat dissipation, electronic components can overheat, leading to reduced performance, shortened lifespan, and even irreversible damage.
Heatsinks come in various shapes and sizes, and they are often found in devices such as computers,smartphones, gaming consoles, and even automotive electronics. These devices generate substantial heat during operation, and without heatsinks, they would be prone to overheating, leading to system failures and potential safety hazards.
In addition to preventing overheating, heatsinks also contribute to overall system reliability. By maintaining optimal temperature levels, heatsinks reduce the risk of thermal throttling, where the device's performance is automatically reduced to prevent damage caused by excessive heat. This ensures that electronic devices can consistently deliver the performance levels expected by users.
Moreover, heatsinks enhance the longevity of electronic components by preventing the degradation of sensitive materials due to prolonged exposure to high temperatures. By efficiently transferring heat away from critical components, heatsinks help extend the lifespan of devices, reducing the need for frequent repairs or replacements.
Types of heatsinks and their applications
Heatsinks come in various types, each designed to meet specific cooling requirements and fit different form factors. The choice of heatsink depends on factors such as power dissipation, available space, airflow, and aesthetic considerations. Here are some common types of heatsinks and their applications:
1. Finned heatsinks: These heatsinks feature a series of fins that increase the surface area for better heat dissipation. They are commonly used in desktop computers, servers, and high-performance gaming systems.Finned heatsinks can be either active, incorporating a fan for forced air cooling, or passive, relying on natural convection for heat dissipation.
2. Heat pipe heatsinks: Heat pipe heatsinks utilize heat pipes, which are sealed copper tubes filled with a working fluid that transfers heat through evaporation and condensation. This type of heatsink is particularly effective at conducting heat over longer distances and is commonly used in laptops, mobile devices, and LED lighting fixtures.
3. Stacked fin heatsinks: Stacked fin heatsinks feature multiple layers of fins, increasing the surface area even further. These heatsinks are often used in high-power applications such as power amplifiers, industrial machinery, and high-end graphics cards.
4. Liquid cooling heatsinks: Liquid cooling heatsinks use a liquid coolant, typically water or a specialized coolant, to transfer heat away from electronic components. This type of heatsink is commonly found in high-performance gaming PCs and overclocked systems that require superior cooling capabilities.
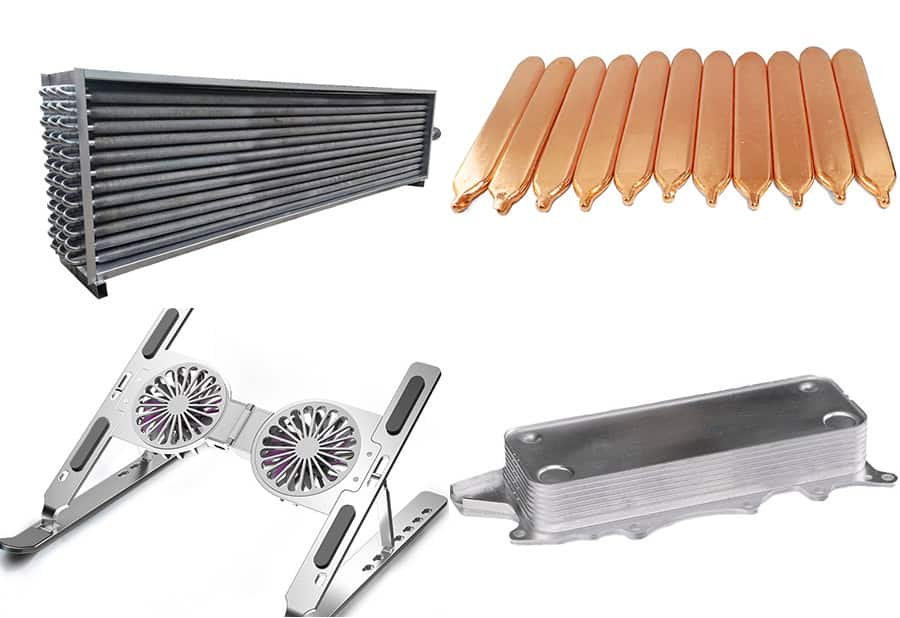
The manufacturing process of heatsinks
The manufacturing process of heatsinks involves several stages, each crucial in ensuring the final product's quality and performance. Let's take a closer look at each step:
1. Design phase: The process begins with the design phase, where engineers determine the heatsink's dimensions, shape, and fin configuration based on the specific cooling requirements. Computer-aided design (CAD) software is used to create detailed 3D models, allowing for precise measurements and simulations.
2. Material selection: Once the design is finalized, the appropriate material for the heatsink is selected.Aluminum and copper are commonly used due to their excellent thermal conductivity. Aluminum heatsinks are lightweight and cost-effective, suitable for most applications. Copper heatsinks, on the other hand, offer superior thermal conductivity but are usually more expensive and heavier.
3. Raw material preparation: The selected material is then prepared for manufacturing. In the case of aluminum heatsinks, aluminum ingots are first melted and then cast into billets or extruded into specific shapes. Copper heatsinks are usually made from copper sheets, which are cut and formed into the desired shape.
4. Machining and shaping: The next step involves machining and shaping the raw material to create the heatsink's core structure. CNC machining techniques are often used to achieve precise dimensions and intricate fin designs. This process may include drilling, milling, turning, and other machining operations.
5. Fin forming: Once the core structure is complete, the fins are formed. This can be done through various methods, such as stamping, folding, or extruding. The choice of fin formation technique depends on factors such as the desired fin density, fin thickness, and manufacturing capabilities.
6. Surface treatment: After the heatsink's core structure and fins are formed, the surface is treated to enhance its performance and aesthetics. Surface treatments can include anodizing, electroplating, powder coating, or painting. These treatments not only provide corrosion resistance but also improve thermal efficiency by increasing the heatsink's emissivity.
7. Assembly and testing: In the final stages of manufacturing, the heatsink is assembled with any additional components, such as heat pipes or fans, if required. Each heatsink undergoes rigorous testing to ensure its thermal performance meets the specified requirements. Testing may involve thermal imaging, thermal resistance measurements, and real-world performance evaluations.
Materials used in heatsink manufacturing
The choice of material plays a crucial role in the overall performance and efficiency of a heatsink. Two of the most commonly used materials in heatsink manufacturing are aluminum and copper.
Aluminum: Aluminum heatsinks are widely used due to their lightweight nature, excellent thermal conductivity, and cost-effectiveness. Aluminum is readily available, making it a popular choice for high-volume production. It is also easy to machine and shape, allowing for intricate fin designs. However, aluminum has a lower thermal conductivity compared to copper, which may limit its use in applications with higher heat dissipation requirements.
Copper: Copper heatsinks offer superior thermal conductivity compared to aluminum, making them ideal for applications that require efficient heat transfer. Copper heatsinks are often used in high-performance systems,such as gaming PCs and high-end servers. However, copper is heavier and more expensive than aluminum,which can be a limiting factor in certain applications.

Other materials, such as graphite, are also used in heatsink manufacturing, particularly in specialized applications where lightweight and high thermal conductivity are essential.
Design considerations for efficient heatsinks
Designing an efficient heatsink involves several considerations to maximize heat dissipation and minimize thermal resistance. Here are some key design considerations:
1. Surface area: Increasing the heatsink's surface area allows for better heat dissipation. This can be achieved by adding more fins, increasing fin density, or utilizing other methods to enhance the surface area, such as heat pipes or stacked fin designs.
2. Fin thickness and spacing: The thickness and spacing between fins impact the heatsink's overall thermal performance. Thinner fins and closer spacing promote better heat transfer. However, these factors must be balanced with manufacturing constraints and airflow requirements to avoid excessive pressure drop or reduced cooling efficiency.
3. Base thickness and contact area: The base of the heatsink, which comes into direct contact with the heat source, should have sufficient thickness and contact area for efficient heat transfer. A larger contact area ensures better thermal conductivity and reduces the thermal resistance between the heatsink and the component.
4. Airflow optimization: Proper airflow management is crucial for effective heat dissipation. The heatsink's design should facilitate the flow of air through the fins, ensuring efficient cooling. This may involve incorporating features such as channels, grooves, or optimized fin shapes to guide the airflow and reduce turbulence.
5. Mounting mechanism: The heatsink's mounting mechanism should provide secure and uniform contact with the heat source. Proper mounting ensures optimal heat transfer and minimizes thermal resistance. Various mounting methods, such as screws, clips, or thermal adhesives, are used depending on the application and space constraints.
Quality control in heatsink manufacturing
Ensuring the quality and reliability of heatsinks is paramount in manufacturing. Quality control measures are implemented throughout the manufacturing process to guarantee consistent performance and adherence to specifications. Here are some common quality control practices in heatsink manufacturing:
1. Material inspection: Raw materials undergo rigorous inspection to verify their quality and suitability for heatsink production. This includes checking for material composition, surface defects, and dimensional accuracy.
2. Process monitoring: Real-time monitoring of critical manufacturing processes, such as machining, forming,and surface treatment, helps identify any deviations or anomalies that may affect the heatsink's performance.
Process parameters, such as temperature, pressure, and machining tolerances, are closely monitored to maintain consistency.
3. Visual inspection: Visual inspection is conducted at various stages of manufacturing to detect any visual defects, such as surface imperfections, scratches, or blemishes. This ensures that only heatsinks meeting the required visual standards are approved for further processing.
4. Thermal performance testing: Heatsinks undergo thorough thermal performance testing to validate their heat dissipation capabilities. This may involve measuring the heatsink's thermal resistance, conducting thermal imaging, or subjecting the heatsink to simulated operating conditions.
5. Reliability testing: Reliability testing is performed to assess the heatsink's long-term performance under various environmental conditions, such as temperature cycling, humidity, and vibration. This helps identify any potential weaknesses or failure modes that may arise during real-world operation.
Advances in heatsink manufacturing technology
Advances in manufacturing technology continue to push the boundaries of heatsink design and production,enabling more efficient cooling solutions. Here are some notable advancements in heatsink manufacturing:
1. Additive manufacturing: Additive manufacturing, also known as 3D printing, has revolutionized the heatsink manufacturing process. It allows for the creation of complex geometries and intricate internal structures that were previously difficult or impossible to achieve using traditional machining methods. Additive manufacturing also offers the flexibility to optimize heatsink designs for specific cooling requirements,resulting in enhanced performance.
2. Microchannel heatsinks: Microchannel heatsinks utilize tiny channels to maximize the surface area available for heat transfer. These channels can be manufactured using advanced microfabrication techniques, such as micro-electro-mechanical systems (MEMS) or laser machining. Microchannel heatsinks offer superior cooling performance and are often used in applications that require high heat dissipation in compact spaces, such as aerospace or automotive electronics.
3. Nanostructured heatsinks: Nanostructured heatsinks incorporate nanoscale features, such as nanowires or nanoporous materials, to enhance heat transfer capabilities. These heatsinks leverage the unique properties of nanomaterials, such as high thermal conductivity or increased surface area, to achieve superior cooling performance. Nanostructured heatsinks have the potential to significantly improve thermal management in advanced electronic devices.
4. Smart heatsinks: Smart heatsinks integrate sensors and control systems to actively monitor and regulate the cooling process. These heatsinks can dynamically adjust their cooling capacity based on real-time temperature data, optimizing the cooling efficiency and adapting to changing operating conditions. Smart heatsinks offer the potential for more precise and energy-efficient cooling solutions.
Common challenges in heatsink manufacturing and their solutions
Heatsink manufacturing is not without its challenges. Here are some common challenges faced in the manufacturing process and the corresponding solutions:
1. Complex geometry: Heatsinks with intricate designs and complex geometries can pose challenges in terms of manufacturing feasibility and cost. Advanced machining techniques, such as CNC machining and additive manufacturing, can help overcome these challenges by providing precise control and flexibility in creating complex shapes.
2. Thermal interface resistance: The interface between the heatsink and the heat source can introduce thermal resistance, negatively impacting heat transfer. To mitigate this, various thermal interface materials, such as thermal pads, thermal greases, or phase change materials, are used to improve thermal conductivity and ensure optimal contact between the heatsink and the component.
3. Cost optimization: Balancing performance and cost is a constant challenge in heatsink manufacturing. By leveraging advanced design and simulation tools, manufacturers can optimize heatsink designs for maximum performance while minimizing material usage and manufacturing complexity. This helps achieve a balance between cost-effectiveness and thermal efficiency.
4. Miniaturization: As electronic devices become smaller and more compact, heatsink manufacturing must adapt to meet the miniaturization requirements. Advanced microfabrication techniques, such as laser machining or MEMS, enable the production of heatsinks with microscale features, suitable for cooling applications in miniature devices.
Conclusion: The future of heatsinks in electronic devices
As electronic devices continue to evolve and become more powerful, the demand for efficient cooling solutions will only increase. Heatsinks, with their ability to dissipate heat and maintain optimal temperatures, will remain an integral part of electronic device design.
Advancements in heatsink manufacturing technology, such as additive manufacturing, microchannel heatsinks, and nanostructured materials, offer exciting possibilities for even more efficient cooling solutions in the future. Smart heatsinks, equipped with advanced sensors and control systems, have the potential to revolutionize thermal management, providing precise and adaptive cooling capabilities.
By understanding the intricacies of heatsink manufacturing, engineers and designers can unlock the full potential of these unsung heroes of the technological world. With optimized cooling solutions, electronic devices can achieve higher performance, improved reliability, and extended lifespans.
Join us as we embark on a deep dive into the world of heatsinks, unlocking their potential and demystifying the manufacturing behind these essential components. From the selection of materials to the intricacies of design and manufacturing, this comprehensive article has provided invaluable insights into the science and artistry of heatsink manufacturing. By harnessing this knowledge, you can make informed decisions to optimize cooling solutions for your unique needs and stay at the forefront of technological advancements.