Welcome to our comprehensive guide on unlocking the power of finned heatsinks. If you're in the world of electronics or engineering, you've likely come across the term heatsink before. But do you truly understand the immense potential of finned heatsinks and how they can revolutionize your thermal management solutions?
In this guide, we will delve deep into the world of finned heatsinks and explore their incredible benefits and applications. Whether you're a professional seeking to optimize heat dissipation in electronic devices or a hobbyist looking to build your own cooling system, this guide will equip you with all the knowledge you need.
We'll start by explaining the fundamental principles of how finned heatsinks work, giving you a solid foundation of understanding. From there, we'll explore different types of heatsinks and their unique designs.You'll discover the science behind heat transfer and how to choose the best heatsink for your specific needs.
So, if you're ready to unlock the full potential of finned heatsinks and take control of your thermal management challenges, let's dive right in. Get ready to optimize performance, increase efficiency, and keep your devices running smoothly with the power of finned heatsinks.
How do finned heatsinks work?
Finned heatsinks are devices designed to dissipate heat generated by electronic components. They are typically made of materials with high thermal conductivity, such as aluminum or copper. The key feature of finned heatsinks is their extended surface area, which allows for efficient heat transfer.
The principle behind finned heatsinks is simple. As electronic devices generate heat, the heatsink absorbs this heat and transfers it to the surrounding air. The extended surface area of the fins increases the contact area between the heatsink and the air, facilitating heat dissipation through conduction and convection.
To enhance the effectiveness of finned heatsinks, manufacturers often incorporate various design elements.One common design feature is the inclusion of multiple fins. These fins increase the surface area even further,maximizing heat dissipation. Additionally, heatsinks may feature heat pipes or thermal pads to enhance thermal conductivity and improve overall performance.
Finned heatsinks are an essential component in a wide range of applications, including computer processors,power electronics, LED lighting, and automotive systems. Their ability to efficiently dissipate heat ensures optimal performance, prolongs the lifespan of electronic devices, and prevents thermal damage.
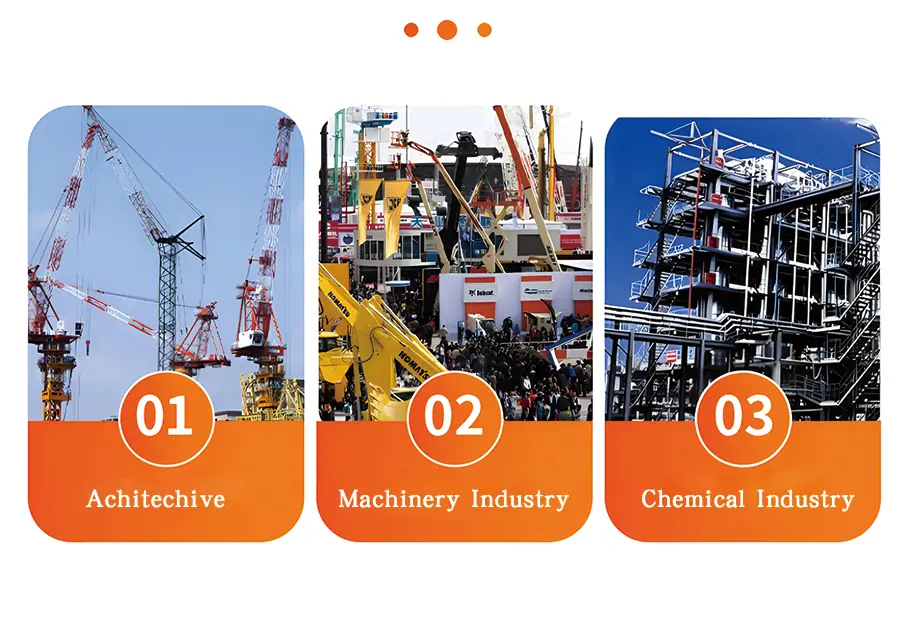
Types of finned heatsinks
Finned heatsinks come in various shapes and sizes, each designed to suit specific thermal management requirements. Let's explore some of the most common types of finned heatsinks:
1. Extruded heatsinks: These heatsinks are manufactured by extruding aluminum or copper into the desired shape. They have a simple design and are cost-effective, making them popular for a wide range of applications.
2. Stamped heatsinks: Stamped heatsinks are created by stamping or pressing sheets of metal into the desired shape. They are lightweight, compact, and offer excellent thermal performance.
3. Bonded-fin heatsinks: Bonded-fin heatsinks consist of individual fins that are bonded to a base plate. This design allows for customization and optimization of the heatsink for specific applications.
4. Skived heatsinks: Skived heatsinks are made by precisely cutting thin layers of metal from a solid block. This manufacturing process results in highly efficient heatsinks with excellent thermal conductivity.
5. Cross-cut heatsinks: Cross-cut heatsinks feature fins that are cut or sliced through their depth, creating thermal paths that enhance heat dissipation.
Each type of finned heatsink has its advantages and limitations. When choosing a heatsink, it's essential to consider factors such as thermal resistance, airflow, space constraints, and application-specific requirements.
Factors to consider when choosing a finned heatsink
Choosing the right finned heatsink for your application requires careful consideration of several factors. Here are some key aspects to keep in mind:
1. Thermal resistance: The thermal resistance of a heatsink determines its ability to transfer heat. Lower thermal resistance results in more efficient heat dissipation.
2. Airflow: The airflow around the heatsink plays a crucial role in heat dissipation. Consider the available airflow in your application and choose a heatsink that can effectively utilize it.
3. Space constraints: The size and shape of the heatsink should align with the available space in your application. It's important to ensure proper fit and clearance to avoid any interference with other components.
4. Material and thermal conductivity: The choice of material for the heatsink affects its thermal conductivity,weight, and cost. Aluminum and copper are commonly used due to their excellent thermal properties.
5. Heat source: Consider the specific heat source in your application. Different components generate varying levels of heat, and the heatsink should be able to handle the thermal load effectively.
By carefully evaluating these factors, you can select a finned heatsink that meets your specific needs and ensures optimal heat dissipation.
Installing a finned heatsink properly
Proper installation of a finned heatsink is crucial to ensure its effectiveness. Here are some steps to follow when installing a finned heatsink:
1. Clean the surface: Before installing the heatsink, make sure the surface of the component is clean and free from any debris or thermal compound residue. Use isopropyl alcohol and a lint-free cloth to clean the surface thoroughly.
2. Apply thermal compound: Apply a thin, even layer of thermal compound on the surface of the component.This helps improve the contact between the component and the heatsink, enhancing heat transfer.
3. Mount the heatsink: Carefully place the heatsink on the component, ensuring proper alignment with any mounting holes or clips. Apply gentle pressure to ensure good contact between the thermal compound, the component, and the heatsink.
4. Secure the heatsink: Depending on the heatsink design, secure it using screws, clips, or other fastening mechanisms. Follow the manufacturer's instructions for proper installation.
5. Check for proper contact: After installation, check for any gaps or uneven contact between the heatsink and the component. Adjust if necessary to ensure uniform contact for optimal heat transfer.
Proper installation of a finned heatsink is essential to maximize its performance and ensure efficient heat dissipation. By following these steps, you can achieve optimal thermal management in your electronic devices.
Common misconceptions about finned heatsinks
Despite their widespread use, there are several common misconceptions surrounding finned heatsinks. Let's debunk some of these misconceptions:
1. Bigger is better: While larger heatsinks generally have more surface area for heat dissipation, size alone does not guarantee better performance. It's crucial to consider factors such as thermal resistance, airflow, and material properties to select an appropriately sized heatsink.
2. More fins mean better cooling: While fins do increase the surface area and enhance heat dissipation, there is an optimal fin density for each application. Too many fins can impede airflow and reduce overall cooling efficiency.
3. Heatsinks eliminate the need for proper ventilation: Heatsinks are designed to complement proper ventilation, not replace it. Adequate airflow is necessary to carry away the heat transferred by the heatsink.
4. All heatsinks are created equal: Heatsinks vary in design, material, and performance characteristics. It's important to choose a heatsink that is specifically tailored to your application's requirements for optimal cooling.
By understanding these misconceptions, you can make informed decisions when selecting and using finned heatsinks.
Maintenance and troubleshooting tips for finned heatsinks
To ensure the longevity and optimal performance of your finned heatsink, regular maintenance and troubleshooting are essential. Here are some tips to keep in mind:
1. Clean regularly: Dust and debris can accumulate on the fins of the heatsink over time, reducing its effectiveness. Regularly clean the heatsink using compressed air or a soft brush to remove any buildup.
2. Check for proper contact: Periodically inspect the heatsink to ensure it is making good contact with the component. Tighten any loose screws or fasteners and reapply thermal compound if necessary.
3. Monitor temperature: Keep an eye on the temperature of the component with a temperature monitoring tool. If you notice a significant increase in temperature, it may indicate a problem with the heatsink or inadequate airflow.
4. Avoid thermal compound spills: When applying thermal compound, be careful to avoid spills or excess compound spreading onto other components. Clean up any spills promptly to prevent potential damage.
5. Consult manufacturer guidelines: Refer to the manufacturer's guidelines for specific maintenance and troubleshooting recommendations for your heatsink model.
By following these maintenance and troubleshooting tips, you can ensure your finned heatsink continues to perform optimally and keeps your electronic devices cool.
Innovations in finned heatsink technology
As technology advances, so does the design and functionality of finned heatsinks. Here are some recent innovations in finned heatsink technology:
1. Advanced fin designs: Researchers and manufacturers are continuously developing new fin designs to improve heat dissipation. These designs, such as wavy or microfin configurations, enhance surface area and promote better airflow.
2. Integrated heat pipes: Heat pipes, which are sealed pipes containing a working fluid, are being integrated into heatsink designs. This allows for more efficient heat transfer and improved overall performance.
3. Thermoelectric cooling: Thermoelectric coolers, also known as Peltier devices, are being incorporated into finned heatsinks to provide active cooling. These devices use the Peltier effect to create a temperature difference across the heatsink, facilitating heat transfer.
4. Liquid cooling integration: Liquid cooling systems, traditionally used for high-performance applications, are being integrated with finned heatsinks. This combination provides enhanced cooling capabilities for applications with higher heat dissipation requirements.
These innovations in finned heatsink technology continue to push the boundaries of thermal management,allowing for more efficient and effective cooling solutions.
Case studies: Successful applications of finned heatsinks
To showcase the practical applications of finned heatsinks, let's explore a few case studies:
1. Computer processors: Finned heatsinks are commonly used in computer processors to dissipate the heat generated during operation. By efficiently cooling the processor, heatsinks prevent thermal throttling and ensure optimal performance.
2. LED lighting: LED lights generate heat during operation, which can affect their performance and lifespan.Finned heatsinks are used to dissipate this heat, ensuring consistent brightness and prolonging the life of the LED.
3. Power electronics: Power electronic components, such as transistors and diodes, generate significant heat.Finned heatsinks are employed to efficiently dissipate this heat, preventing thermal damage and ensuring proper functioning.
4. Automotive systems: In automobiles, finned heatsinks are used to cool various components, including power modules, batteries, and engine control units. Effective thermal management ensures reliable performance and extends the lifespan of these critical systems.
These case studies demonstrate the versatility and effectiveness of finned heatsinks in a wide range of applications, making them an indispensable tool for efficient thermal management.
Conclusion: Harnessing the power of finned heatsinks for optimal cooling
Finned heatsinks are a powerful tool for efficient thermal management in electronics and engineering applications. By understanding their principles, types, and selection criteria, you can harness their full potential and unlock optimal cooling performance.
Remember to choose the right finned heatsink for your specific needs, considering factors such as thermal resistance, airflow, and space constraints. Proper installation, regular maintenance, and troubleshooting are essential to ensure long-term performance and reliability.
As technology advances, so do the innovations in finned heatsink technology. Stay informed about the latest advancements and incorporate them into your thermal management solutions for even better cooling performance.
With the knowledge gained from this comprehensive guide, you are now equipped to optimize performance,increase efficiency, and keep your devices running smoothly with the power of finned heatsinks. Embrace the potential of finned heatsinks and take control of your thermal management challenges today!